Commodity Number :
352-321-524-040
Commodity Name :
VM Fanuc 0i-TF+C 2024 Professional Version
Commodity Introduction :
Realistic CNC Controller Function Panel, Modularized Machine Operation Panel, and Machine Simulation. Excellent tool for CNC controller recognition and practicing tool offset.
Use Version :
Subscription Plan:
Commodity Price :
Product Specifications
1 CNC Controller Function
1.01 CNC Controller Simulation Fanuc 0i-TF +C +Y Mill Turn
1.02 The Operation Panel Function is the complete emulation based on the actual CNC machine operation panel
1.11 Position Display [POS]:
(1) Absolute: absolute coordinates, machine coordinates, distance to go
(2) Relative: relative coordinates, machine coordinates, distance to go
(3) All: relative coordinates, absolute coordinates, machine coordinates, distance to go
(4) Handle: input unit, output unit, relative coordinates, distance to go
(5) Monitor: Load Meter, Spindle Load, Spindle Speed
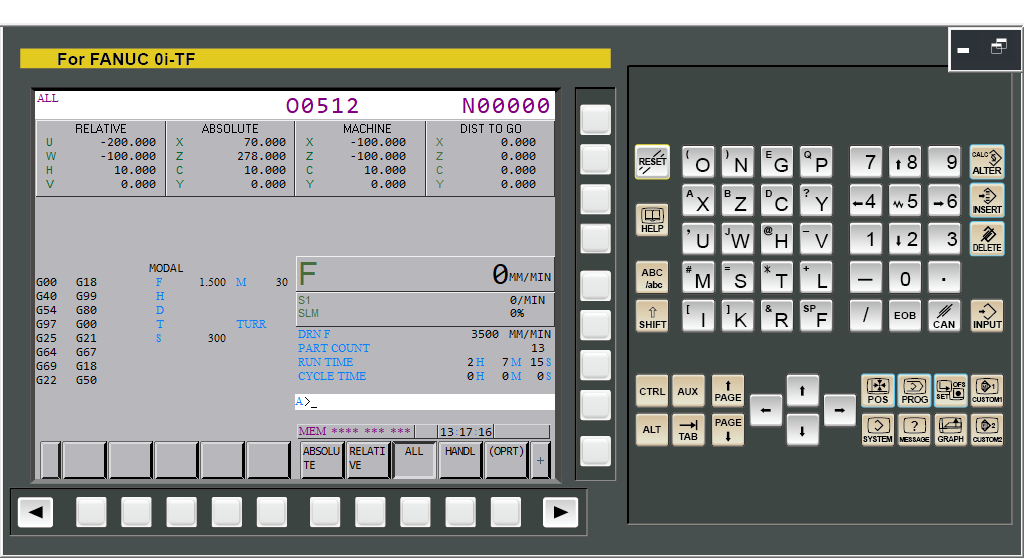
1.12 Program function[PROG]:
(1) Program: edit and display current program
(2) Folder: display the list of parts programs in the record
(3) Next: Display the current command value and the next command value
(4) Check: display program, position and status
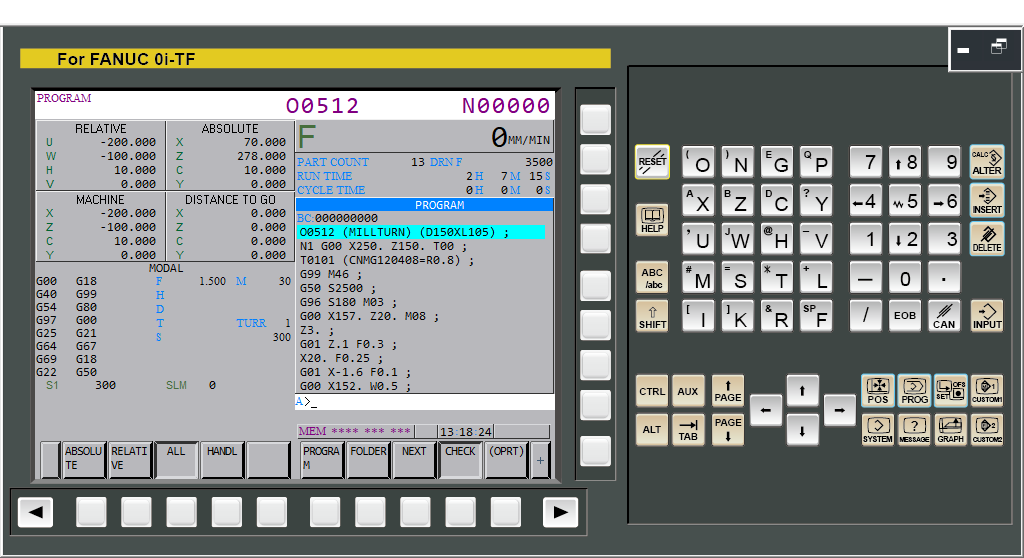
1.13 Tool compensation[OFS/SET]:
(1) Offset: tool geometry and wear offset view and settings
(2) Settings: parameters input permission, data transmission unit settings
(3) Coordinates: work coordinates view and settings
(4) Work shift: work coordinates shift value view and settings
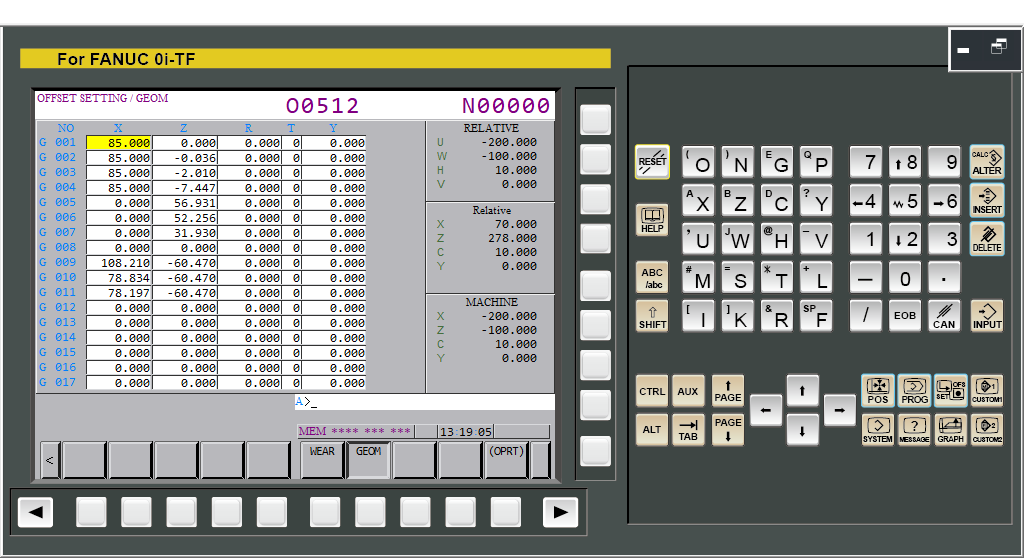
1.14 System parameters [SYSTEM]:
(1) Parameters: system parameters view and settings
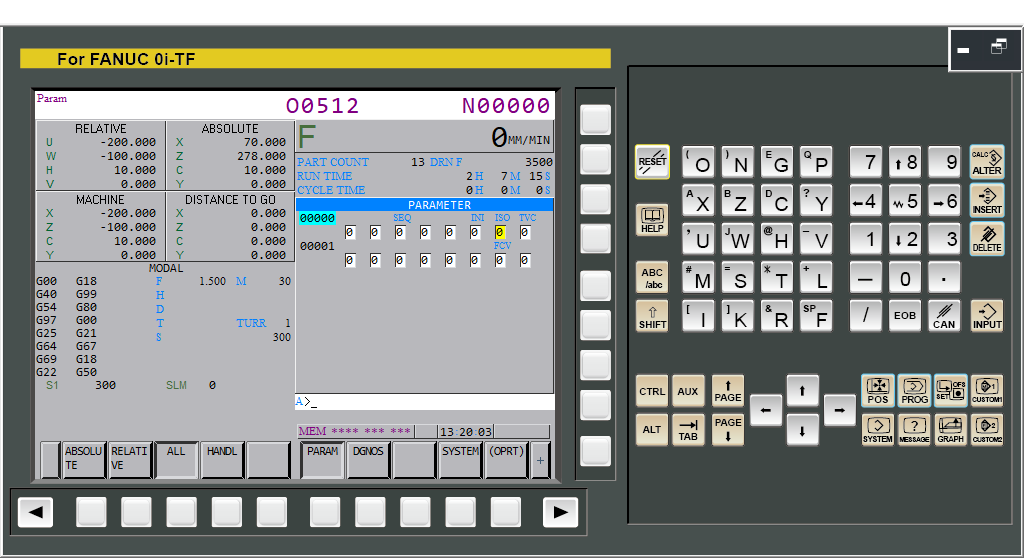
1.15 Message [MESSAGE]:
(1) Alarm: Alarm message
1.03 Alarm display, the alarm codes show the same codes as in the machine
(1) E.g.: X axis over travel, the alarm code shows: ”OT0500 OVER TRAVEL:+X”. To clear the alarm , move X axis to the proper position and press [RESET] to clear the alarm
(2) E.g.: EX1211 EMERGENCY STOP, release the emergency button to clear alarm
(3) System records the time and the error codes whenever the alarm message is displayed
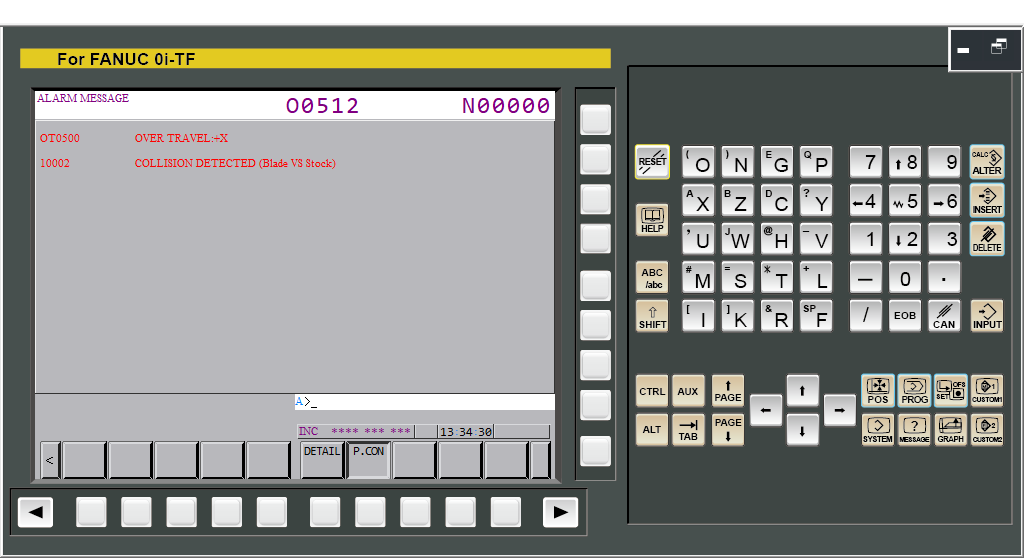
1.04 RJ45 interface information transmission function
Standard Version Features (included)
1.31 System parameters [SYSTEM]:
(1) MACRO: Variable view and settings
1.32 Message [MESSAGE]:
(1) Alarm: Operator message
(2) History: Display previous alarm contents
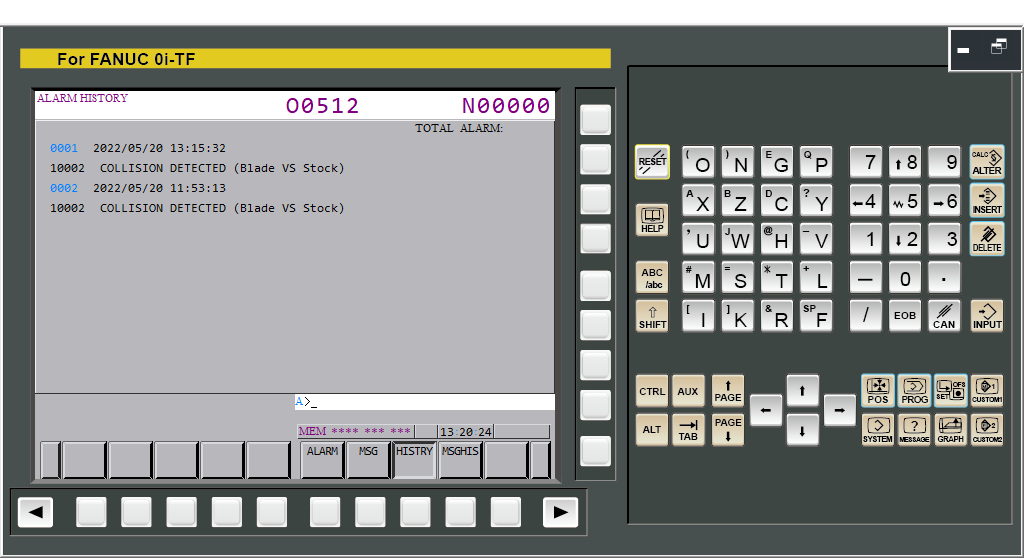
2 CNC Machine Operation Panel Function
2.01 Mode Select Function
(1) [EDIT] Program edit mode – Edit program content
(2) [AUTO] Auto execution mode – Program executes automatically
(3) [MDI] Manual Data Input – For parameter settings and temporary input program
(4) [HANDLE] Handle mode – Using handwheel to move and adjust position
(5) [JOG] Cutting feed mode – Using axis button to feed
(6) [RAPID] Rapid mode – Using axis button to move rapidly
(7) [ZRN] Zero Point Return – return each axis to Home Position
2.02 Rapid Speed adjustment button, Feed speed adjustment button, Spindle speed adjustment button
2.03 Optional block skip [B.D.T], Single block execution [S.B.K], Optional stop [M01], Start [CYCLE START], Stop [FEED HOLD]
2.04 Spindle forward, Spindle stop, Spindle reversal
2.05 Program lock, Emergency stop, Tool change button
2.06 Axis movement buttons: [+X], [-X], [+Y], [-Y], [+Z], [-Z], [+C], [-C] Release collision button, axis return signal
2.07 Handwheel, Handwheel Feedrate Knob, Handwheel Axis Selection Knob
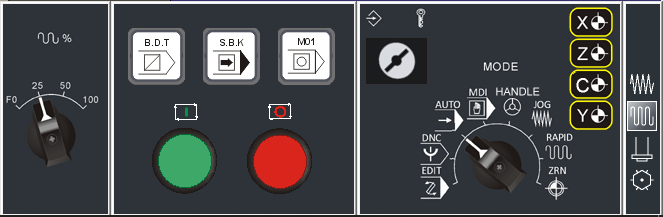
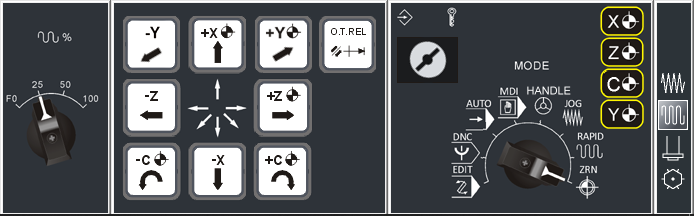
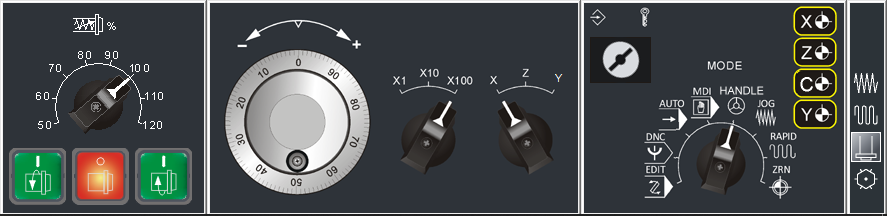
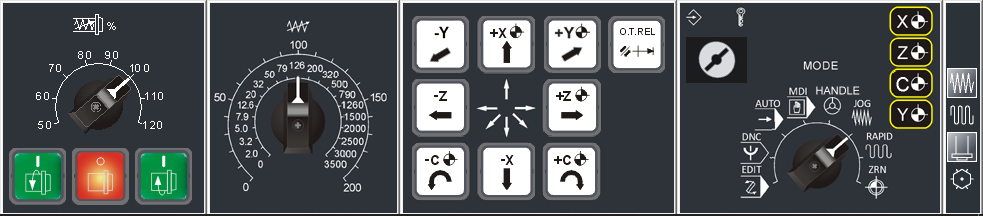
Standard Version Features (included)
2.08 Coolant
Professional Version Additional Features
2.09 Working light button, Safety door open/ close
3 CNC Machine Simulation for Mill Turn
3.01 Based on 3D Solid construction, the machine model of Horizontal Turning (Single spindle and Single turret), including chuck, jaw, power turret, tool
Travel: X Axis 270 mm, Y Axis 110 mm, Z Axis 560 mm
Rapid: X Axis 20 m/min, Y Axis 20 m/min, Z Axis 24 m/min, C Axis 24 rpm
Max Feedrate: X Axis 6 m/min, Y Axis 6 m/min, Z Axis 8 m/min, C Axis 24 rpm
3.02 Simulate whole CNC machine with physical machine controlling panel and dynamic interactive simulation
3.03 Collision detection function: tool and material. If the tool isn’t rotating, the contact between the tool and the material will be considered a collision
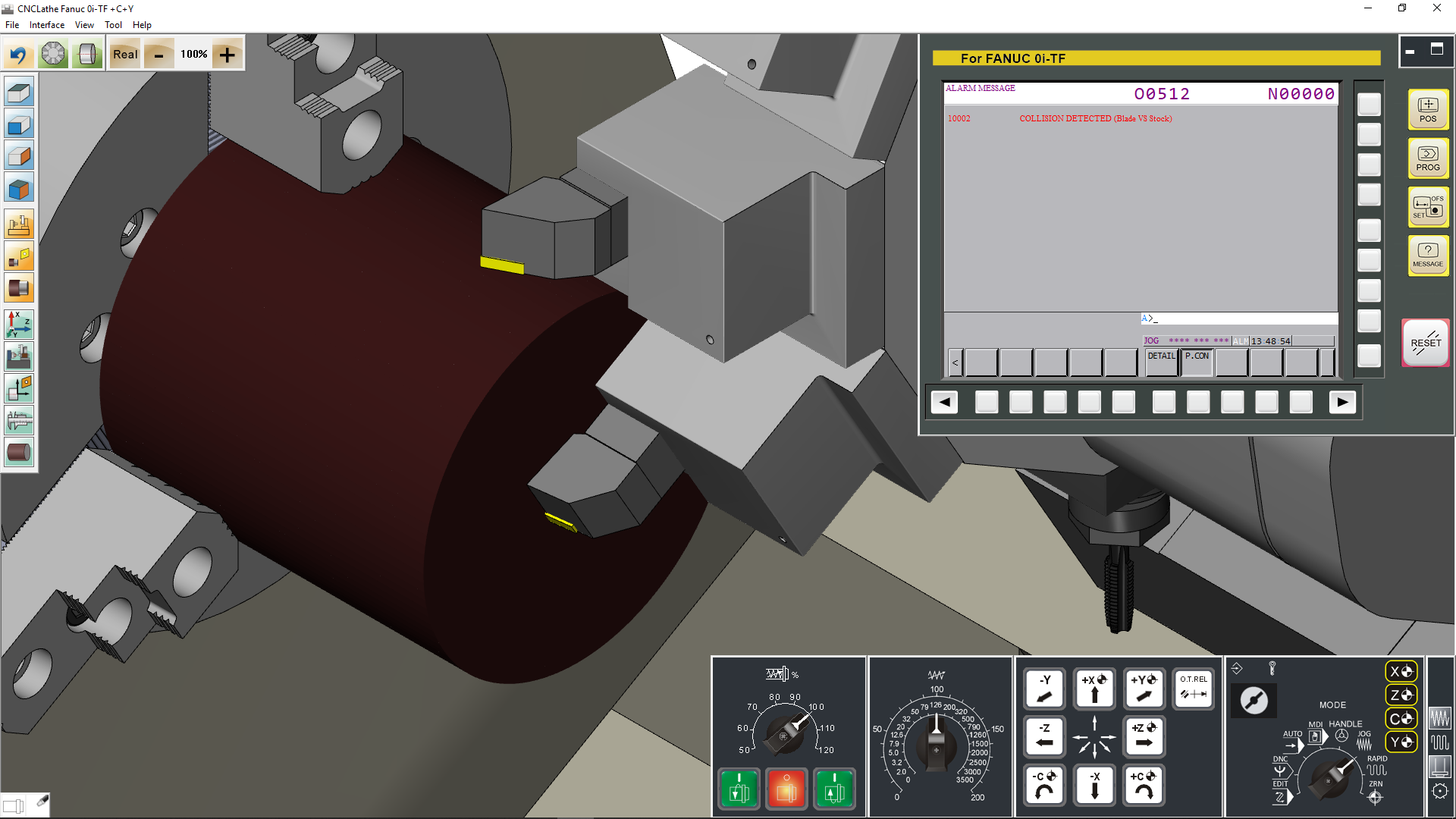
3.04 Simulation Speed Adjustment: 50%, 100%, 250%, 500%
3.05 Audio on/off, system volume adjustment
3.06 Workpiece material setting
Diameter, Max Diameter= 250mm
Length, Max Length=450mm
3.07 Turning tool setting: Diamond (80°, 55°, 35°), Trigon (80°), Triangle (60°), Round, Groove, Ball Nose, Thread, Drill, High Speed Drill, Screw Tap, End Mill, Chamfer, Spot drill
3.08 Turret setting: Tool install, modify, delete
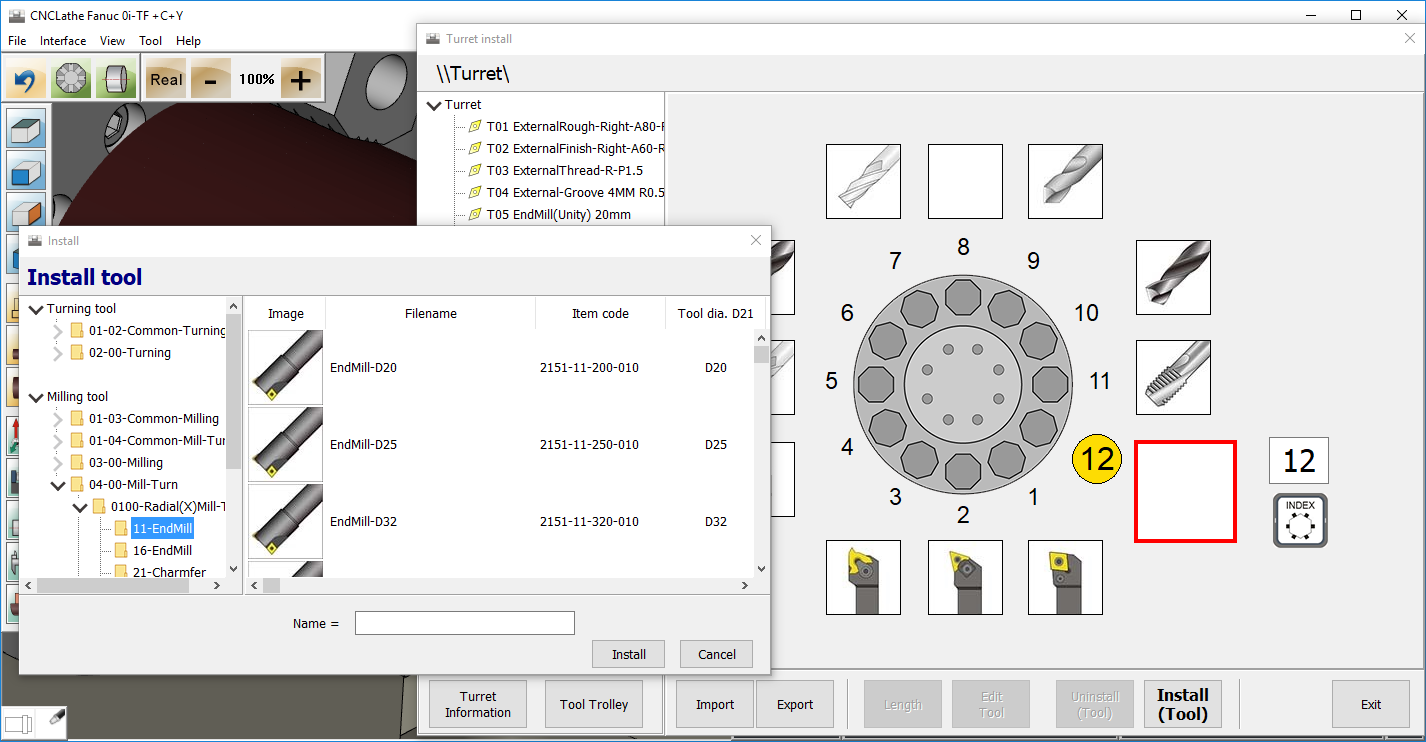
3.09 Standard view : Top (XY), Front (ZX), Side, (YZ), 3-Dimension (ISO)
3.10 Common zoom view: Material view, Table view, Machine view
3.11 Free operation view: Shift, Rotate, Zoom in/out
Standard Version Features (included)
3.21 Based on 3D Solid construction, the machine model of Horizontal Turning (Single spindle and Single turret), including Machine bed, spindle head, chuck, jaw, power turret, tool
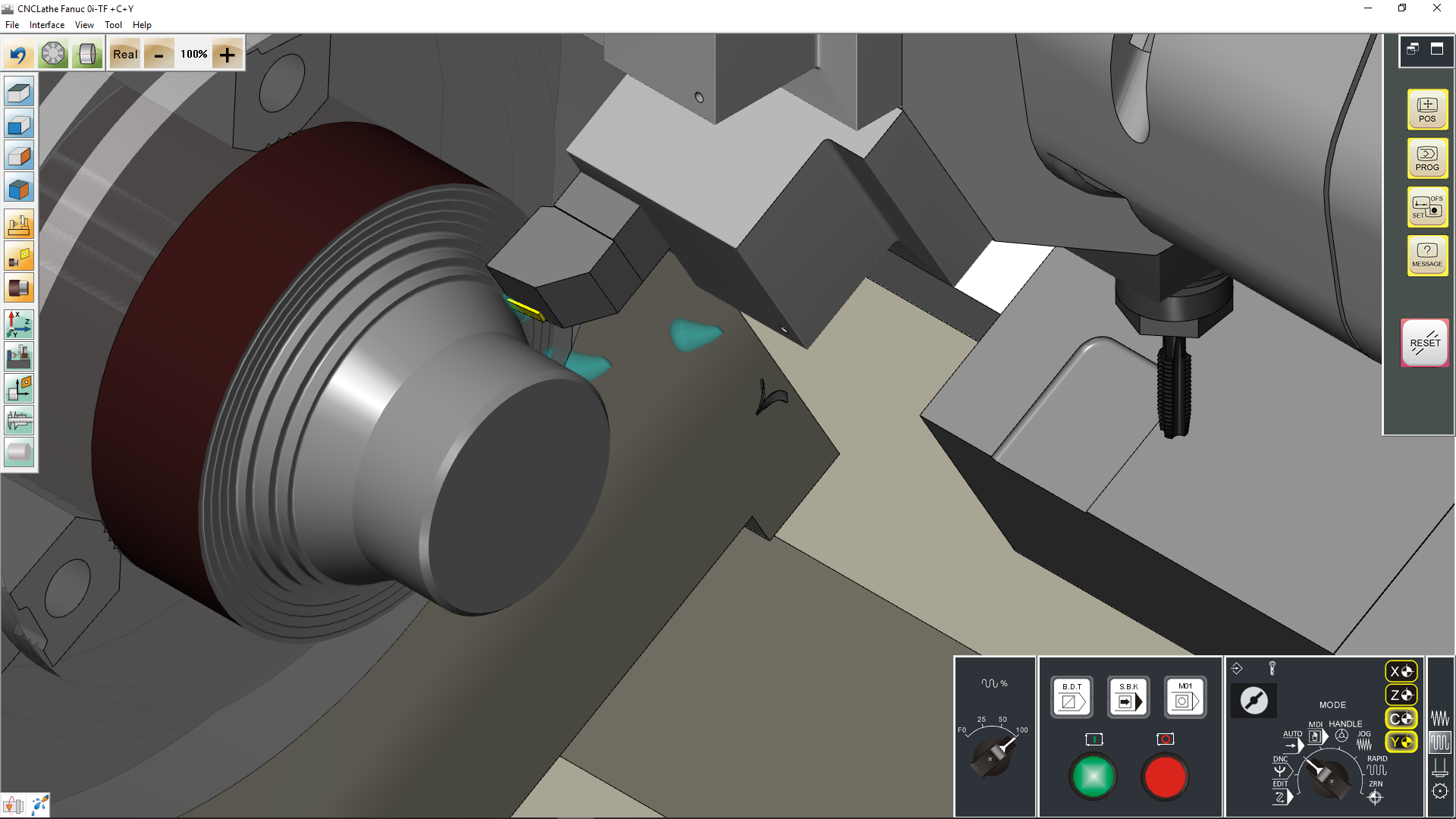
3.22 Simulated design including coolant fluid, chips spattering when cutting the workpiece, audio (tool movement, cutting sound effect, spindle rotation, alarm)
3.23 Collision detection function: tool and material, spindle, jaw, tailstock collision detection
3.24 Workpiece linear measurement function: diameter, thickness, length
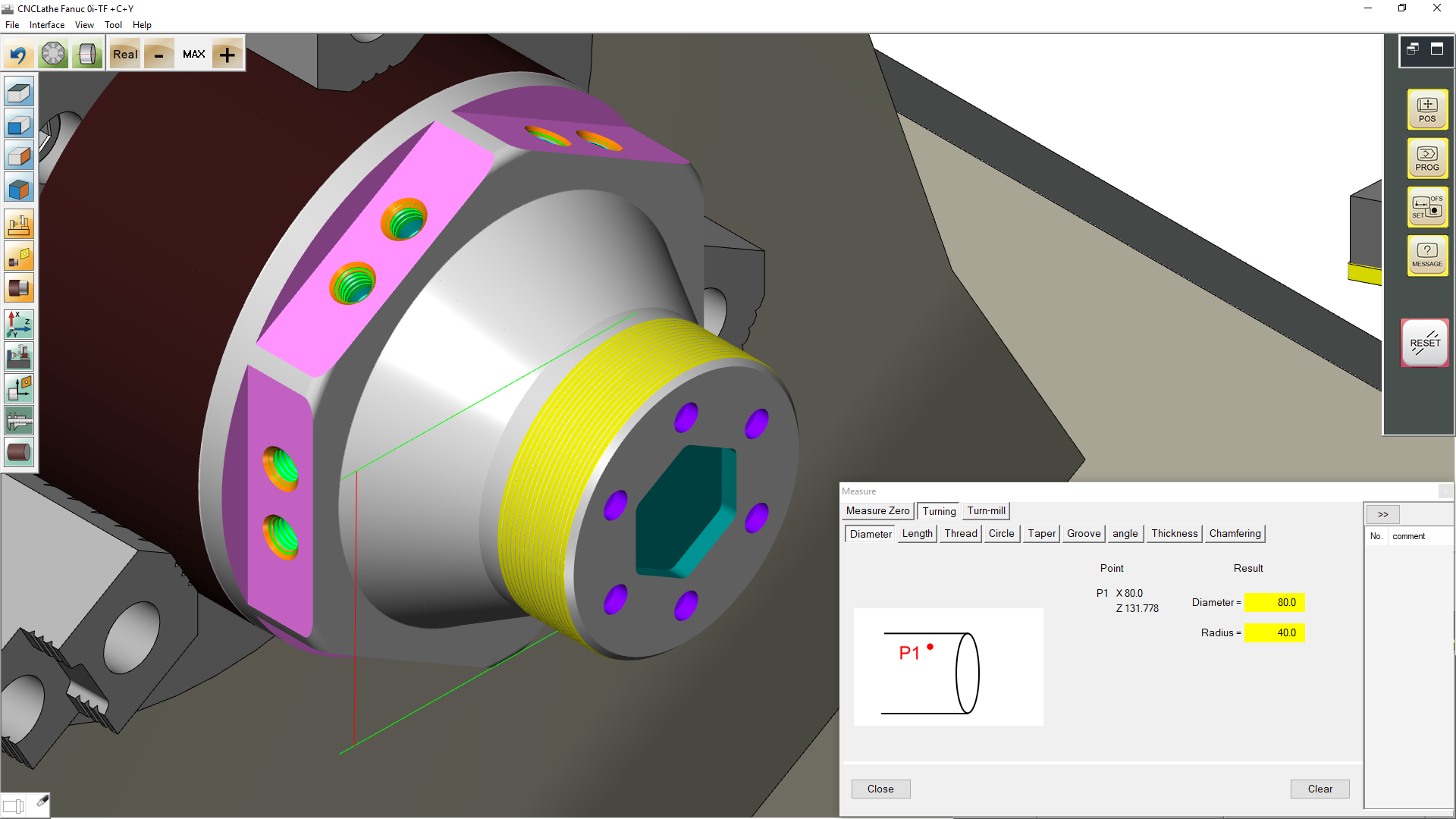
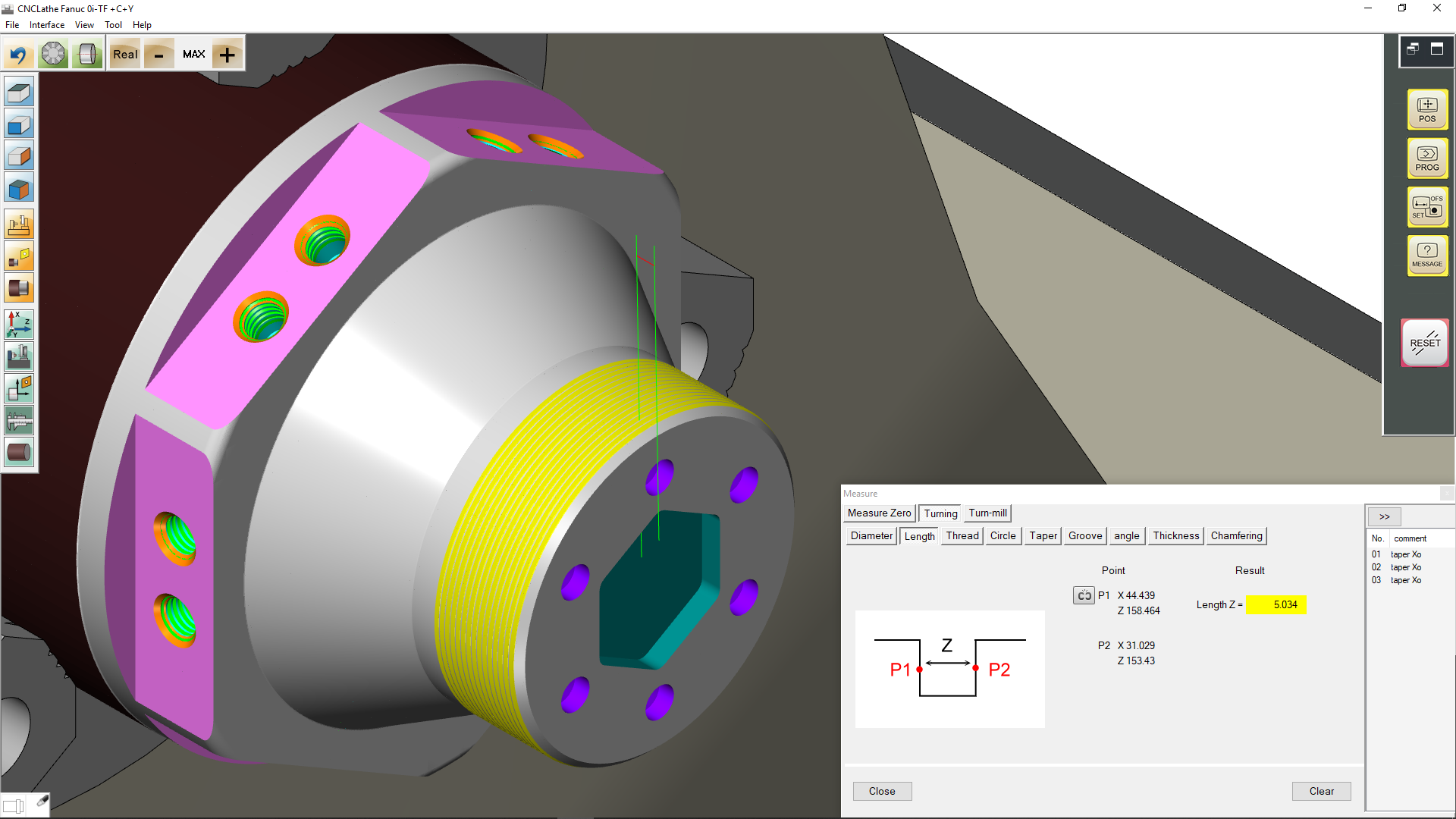
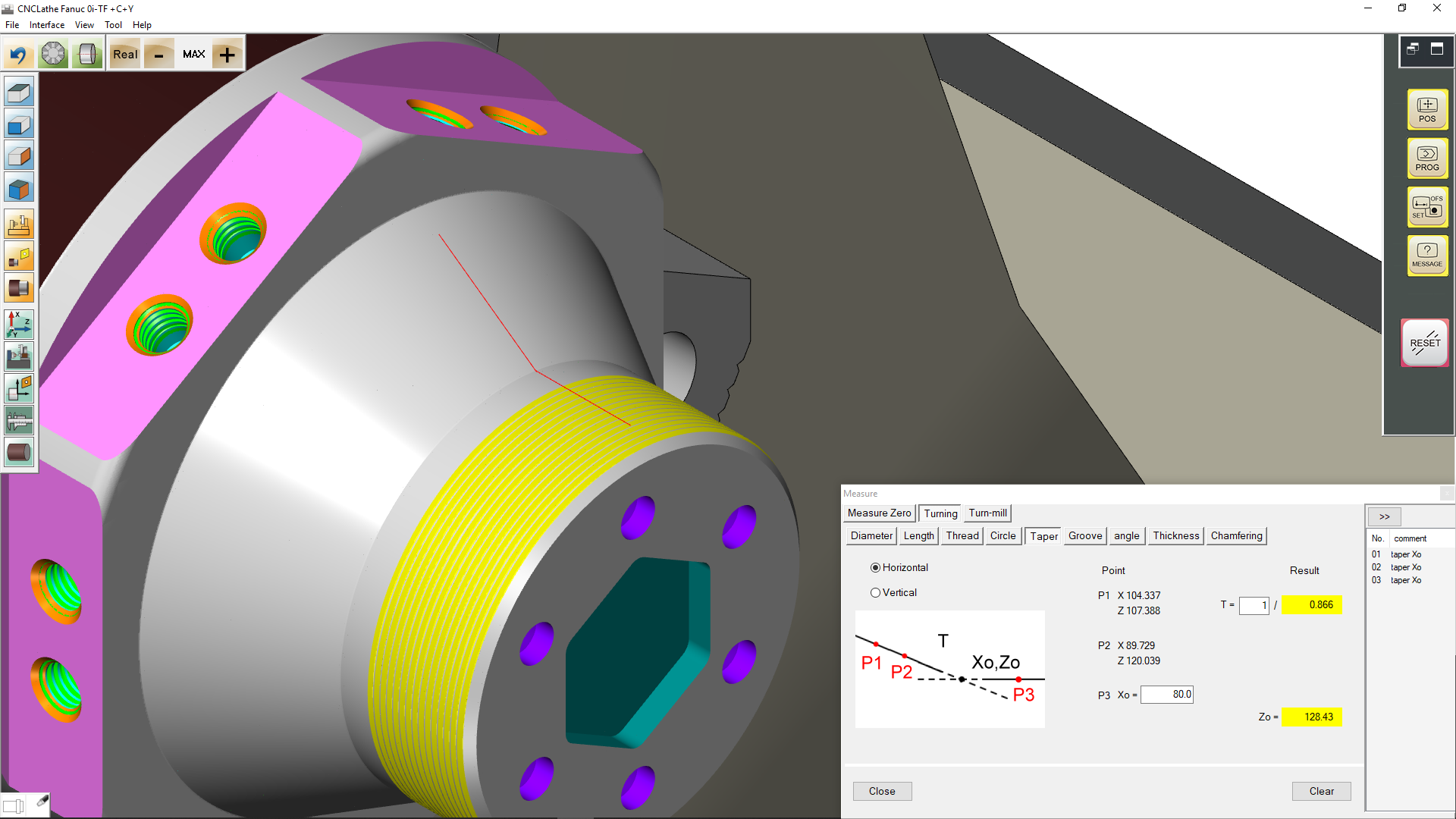
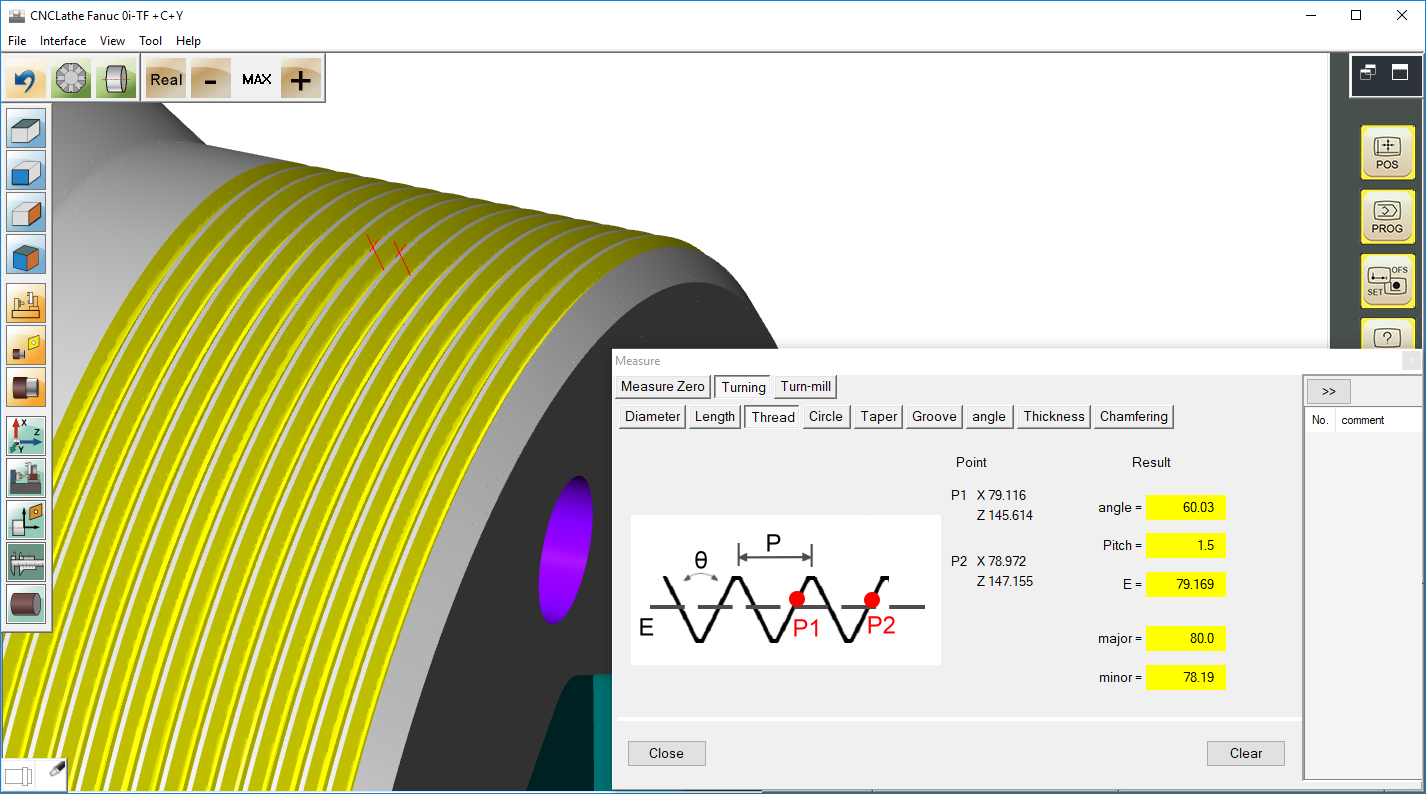
3.25 Quick reset to Factory Setting
3.26 CNC Program import/export function
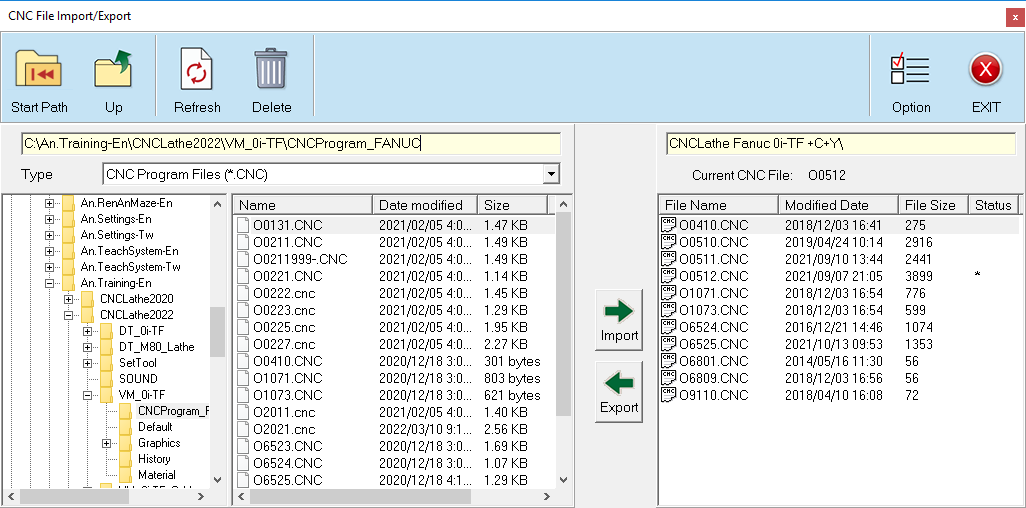
3.27 Install/uninstall spindle tool
3.28 Save and import configuration to completely save and resume the settings status as a reference of examination and correction
Professional Version Additional Features
3.31 Based on 3D Solid construction, the machine model of Horizontal Turning (Single spindle and Single turret), including Machine bed, sheet metal, automatic door, spindle head, chuck, jaw, power turret, tool, tailstock, live center
3.32 Machine case Display/Hide
3.33 Tool offset function
Workpiece Offset: Display material center line, color change of tool while cutting
Arm for contact tool setter: Auxiliary function for tool offset
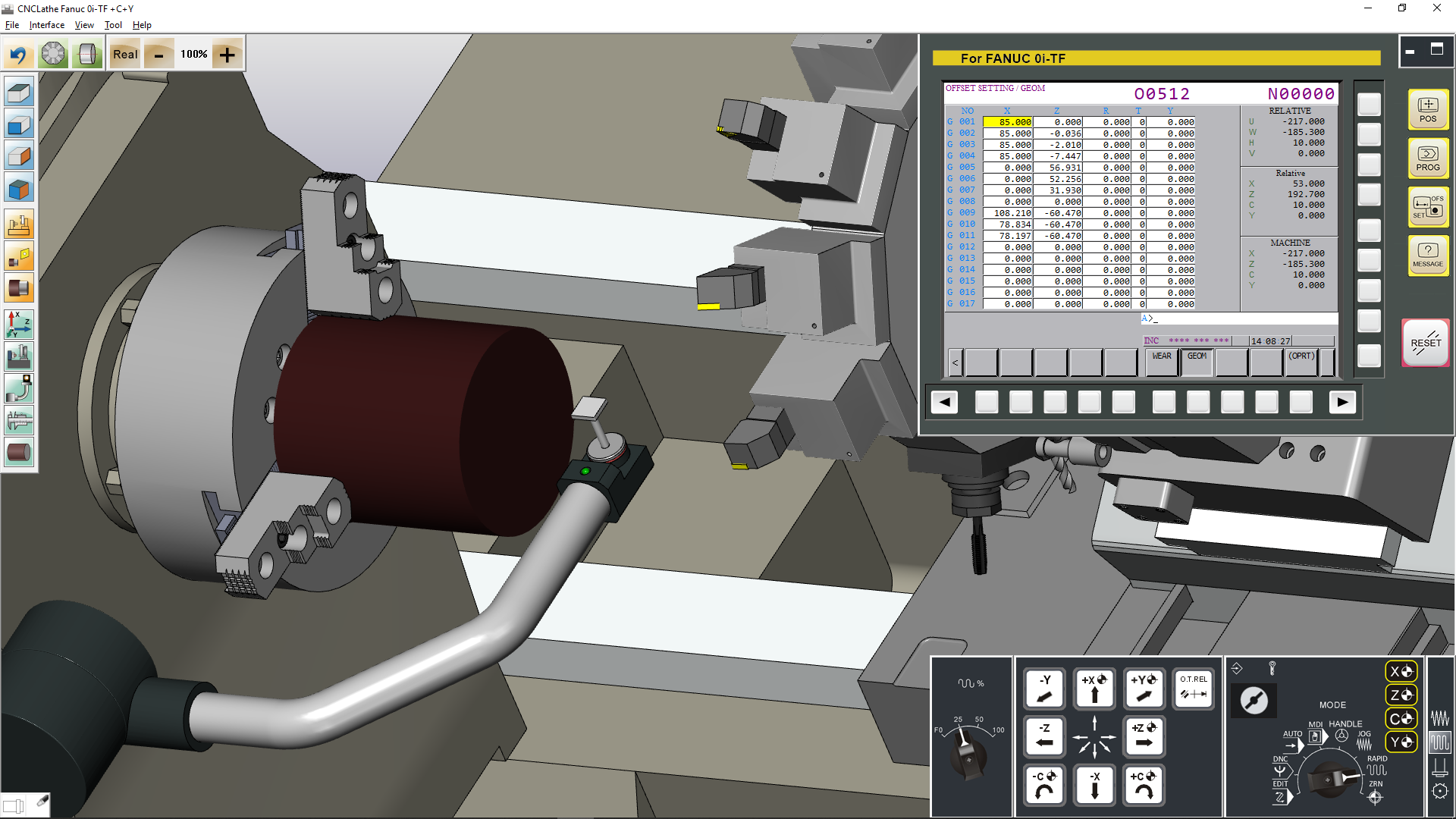
3.34 Jaw Install/Uninstall, Jaw Fix dynamic simulation(DT, TM):
Jaw install/uninstall, Soft jaw select/ install, Soft jaw position adjustment, workpiece comparison, forming ring, soft jaw cutting, workpiece AB-side turning clamping adjustment
3.35 Program zero point display according to different tool offset dynamic position
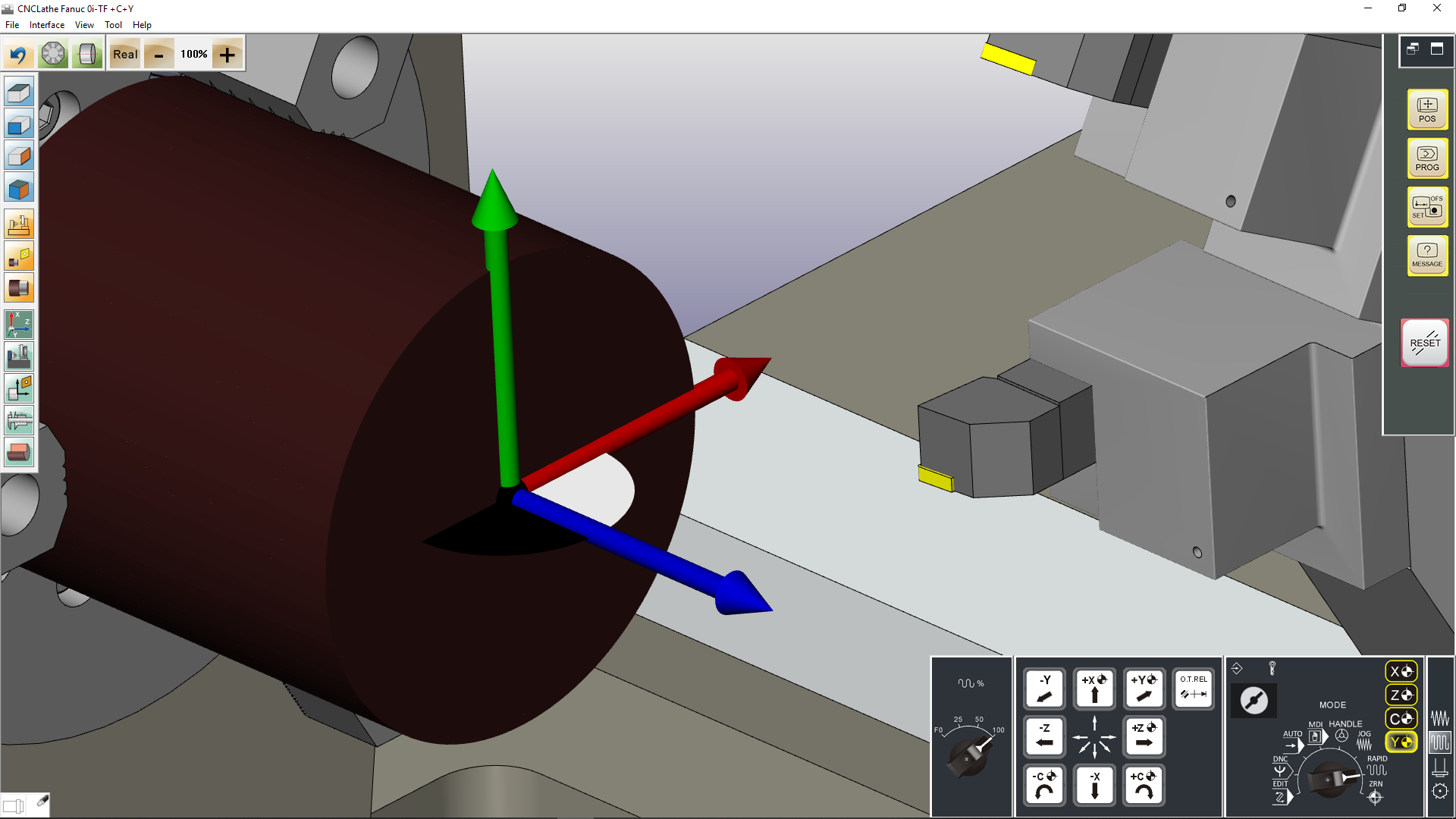
3.36 Workpiece and material: save and load function (format: STL)
3.37 Material setting: inner hole dimension setting, jaw clamp setting
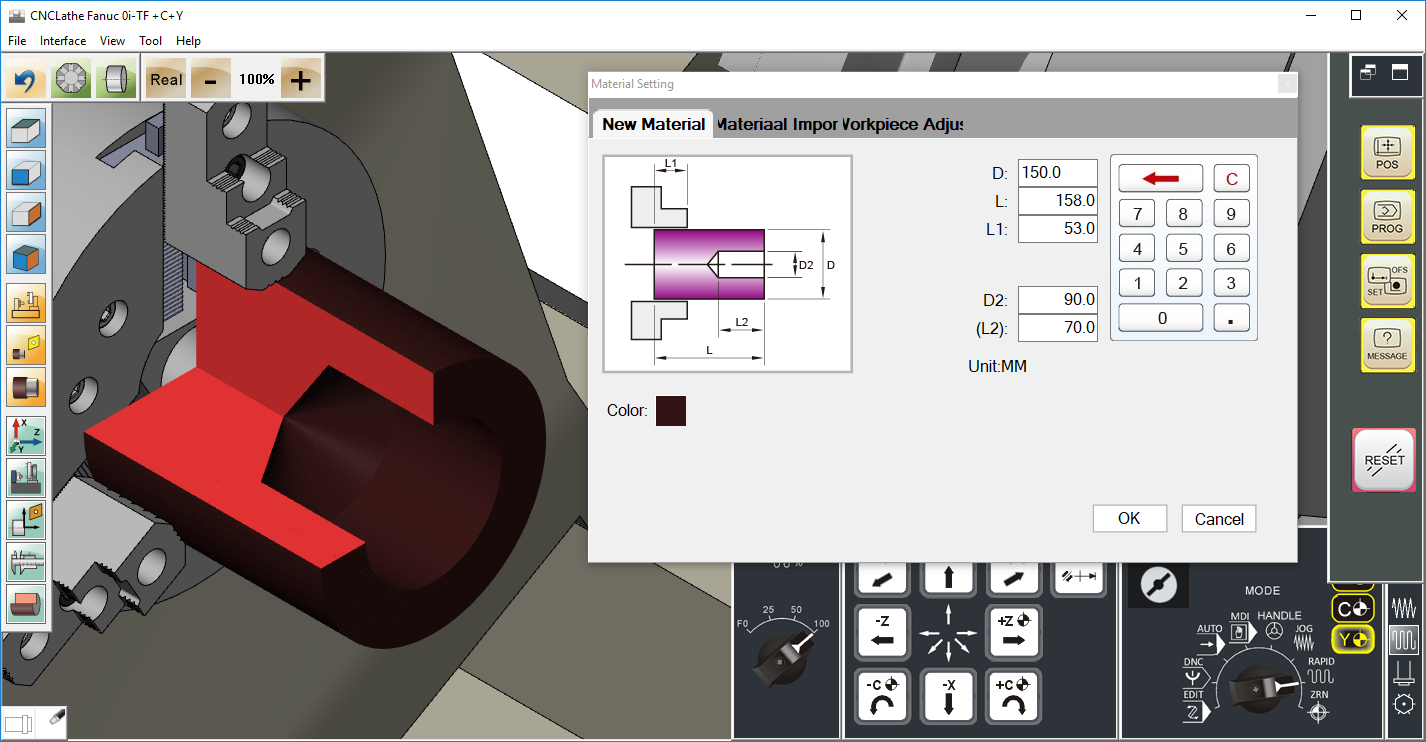
3.38 Tool setting: add, modify, delete, tool data import/export
3.39 Turret Install: Import/Export, Common Turret
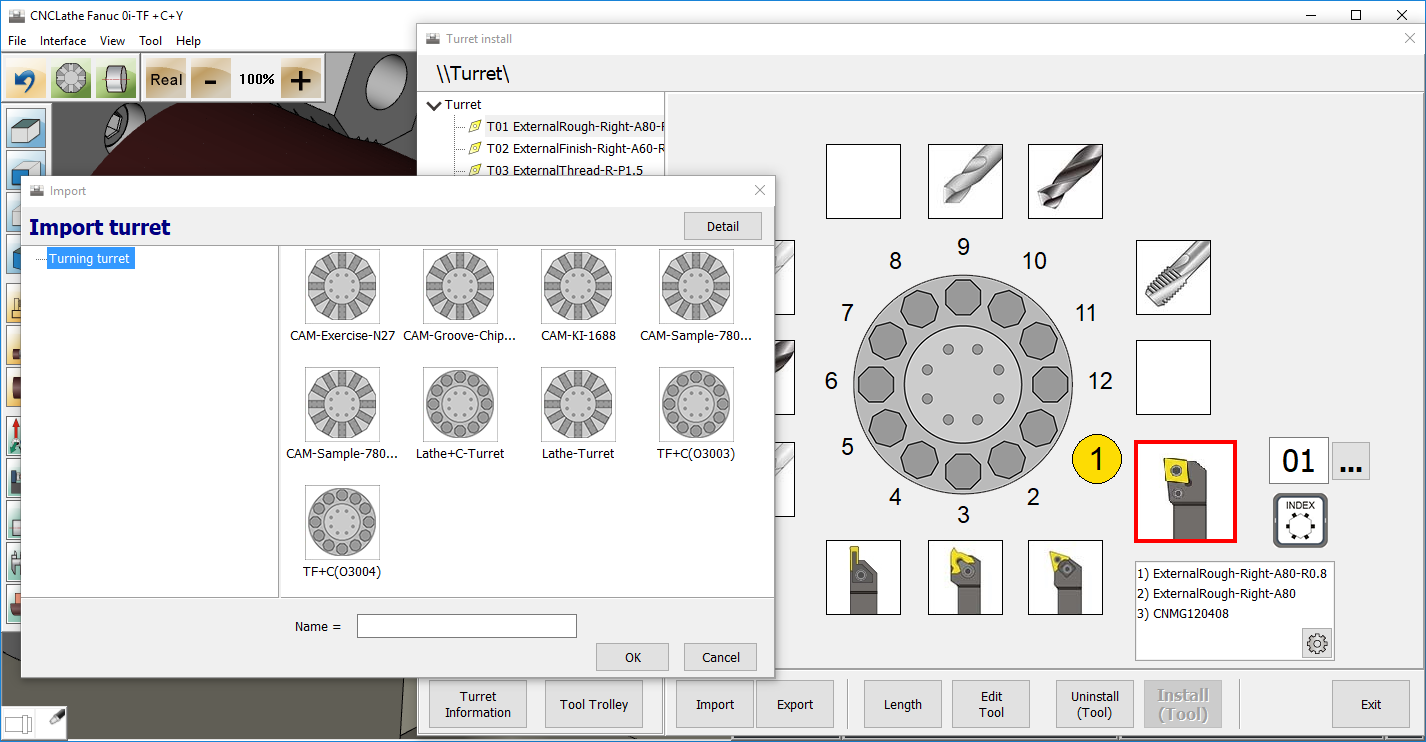
3.40 Simulation Speed Adjustment:
10%, 50%, 100%, 160%, 250%, 500%, 900%, 990%, MAX
3.41 Limit the simulation speed within the range of 500% to help students with their program check and execution
3.42 Equipped with machine produce status and immediate monitoring management system
3.43 Collision detection:
Tool and material, jaw, spindle, tailstock, collision detection
Turret and material, jaw, spindle, tailstock, collision detection
3.44 The Alarm displays if the safety door is opened during simulation
3.45 Material profile display: 1/2 and 1/4 profile function
4 CNC Program Simulation for Mill Turn
4.01 G Code function
(1) Interpolation: G00 G01 G02 G03
(2) Dwell: G04
(3) Plane Selection: G17 G18 G19
(4) Workpiece dimension: Input in inch/mm: G20 G21
(5) Return to reference position: G27 G28 G30
(6) Local coordinates setting: G52
(7) Machine coordinates selection: G53
(8) Workpiece Coordinate: G54, G55, G56, G57, G58, G59
(9) Feed per minute/ revolution: G98, G99
(10) Speed control: G96, G97
(11) Maximum speed: G50
4.02 M Code auxiliary function
(M00) Program stop (M03) Spindle forward (M30) end of program
(M01) Optional stop (M04) Spindle reversal
(M02) End of program (M05) Spindle stop
(M203) Mill Turn axis forward, (M46) Common spindle mode
(M204) Mill Turn axis reverse, (M45) Cs axis mode (Enter C Axis)
(M205) Mill Turn axis stop
Standard Version Features (included)
4.21 G Code function
(1) Cylindrical Interpolation: G07.1、G107
(2) Polar Coordinate Interpolation: G12.1、G13.1、G121、G113
(3) Cutter compensation: G40、G41、G42
(4) Cutting cycle: G70, G71, G72, G73, G74, G75, G76, G90, G92, G94
(5) Cycle for drilling & tapping: G80, G83, G84, G85, G87, G88, G89
(6) Chamfer command settings using comma (parameter)
(7) Omitting the use of decimal point of address (parameter)
(8) Using G Code group setting (parameter)
(9) Tool Radius Compensation: G40 G41 G42
4.22 M Code auxiliary function
(M08) Coolant fluid on (M98) Call Subprogram
(M09) Coolant fluid off (M99) End of Subprogram
Professional Version Additional Features
4.31 G Code function:
(1) Support G01 Angle A command
(2) Spindle speed fluctuation detection: G25、G26
(3) Coordinates selection: G50
(4) MACRO mode call: G65, G66, G67
(5) Support G01with auto Chamfer and Radius of any included angle
(6) Complete support for G71 Canned CycleII multiple stages rough cutting
4.32 M Code functions
(M25) Door close
(M26) Door open
4.33 MACRO program function
(1) Program variable: Local variable, Common variable, System variable
(2) Arithmetic command:
addition +, subtraction -, multiplication x, division /
SIN, COS, TAN, SQRT square value, ABS Absolute value
(3) Logic Operations:
EQ equal to, NE not equal to, GT greater than, LT less than, GE greater than or equal to, LE less than or equal to
(4) Conditional Branches:
(a) Unconditional branches GOTO n
(b) Conditional branches IF [conditional] GOTO n
(c) Repetitive execution WHILE [conditional] DO m