Commodity Number :
362-221-522-040
Commodity Name :
VM Siemens 828D Lathe 2022 Professional Version
Commodity Introduction :
Realistic CNC Controller Function Panel, Modularized Machine Operation Panel, and Machine Simulation. Excellent tool for CNC controller recognition and practicing tool offset.
Use Version :
Subscription Plan:
Commodity Price :
Product Specifications
1 CNC Controller Operation Panel Function
1.01 SINUMERIK 828D Turning CNC Controller Simulation
1.02 The Operation Panel Function is the complete emulation based on the actual SINUMERIK 828D sl CNC machine operation
(1) [Machine] Machining operation: display machine coordinate, absolute coordinate and machining status
(a) (AUTO) Overstore, program control, block search, settings
(b) (MDA) Load MDI, save MDI, program control, settings
(c) (JOG) TSM, measure workpiece, measure tool, position,
stock removal, settings, changeover inch
(2) [PROGRAM] Program editing:
Function key (edit):
Select tool, search, mark, copy, paste, cut, renumbering, settings, exit
Cycle command edit (drilling):
Centering, drilling reaming, deep hole drilling, boring, thread, positions, position repetition
Cycle command edit (turning):
Stock removal. groove, undercut, thread, thread longitudinal, thread tapper, thread face, thread face, cutoff
Cycle command edit(other): blank, sub-program
Cycle command edit(contour turning):
New contour, contour call, stock removal, cut residual stock, grooving, groove reside, plunge turning, plunge turn. residual
(3) [OFFSET] Tool offset:
(a)Tool offset (Geometry):
Tool list, tool measure, edge, unload,
magazine selection, delete tool, sort
(b)Tool offset (Wear) : Sort, search
(c)Work set: Set W0, active, overview, base,
G54..G57, details
(d)Working area limitation
(4) [PROGRAM MANNGER] Program management: execute, new, open, mark, copy, paste, cut, search, properties, delete
(5) [ALARM] Alarm: Alarm list, Alarm log
2 CNC Machine Operation Panel
2.01 Mode Select Button Function
(1) [AUTO]Auto execution mode
- Program executes automatically
(2) [MDA] Manual Data Input
- For parameter settings and temporary input program
(3) [JOG]Cutting feed mode
- Using axis key to feed
(4) [RAPID]Rapid mode
- Using axis key to move rapidly
2.02 Rapid override
2.03 [CYCLESTART], [CYCLESTOP], [SINGLE BLOCK], [RESET]
2.04 Spindle reversal, Spindle stop, Spindle forward
2.05 Program lock, Emergency stop, Magazine change button, Coolant
Safety door open/ close
2.06 Axis movement buttons [X], [Z], positive[+], negative[-], [RAPID], Reset button, axis return signal [REF.POINT]
2.07 Manual handle button[MPG], Physical manual handle,
manual handle rate button, manual handle axis button
3 CNC Turning Machine Simulation
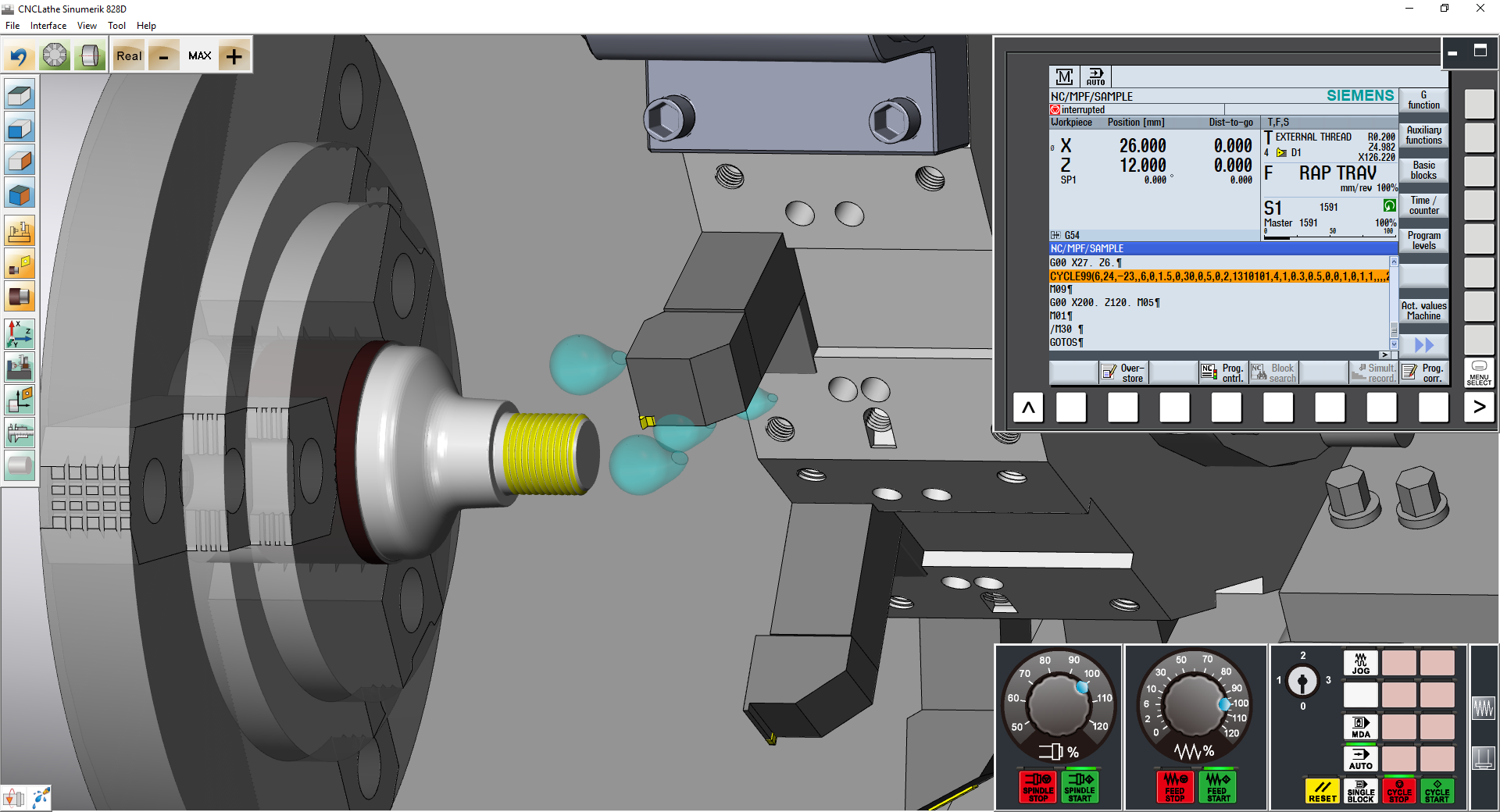
3.01 Based on 3D physical construction, the machine model of Horizontal Turning-Single spindle and turret including: chuck, jaw, turret, tool, tailstock, live center
Travel:X axis 320 mm, Z axis 650 mm
Rapid:X axis 20 m/min,Z axis 24 m/min
Max Cutting Feed: X axis 6 m/min, Z axis 8 m/min
3.02 Simulate whole CNC machine with physical machine control panel and dynamic interactive simulation
3.03 Collision detection function: tool and material.
If the tool isn’t rotating, the contact between the tool and the material will be considered a collision
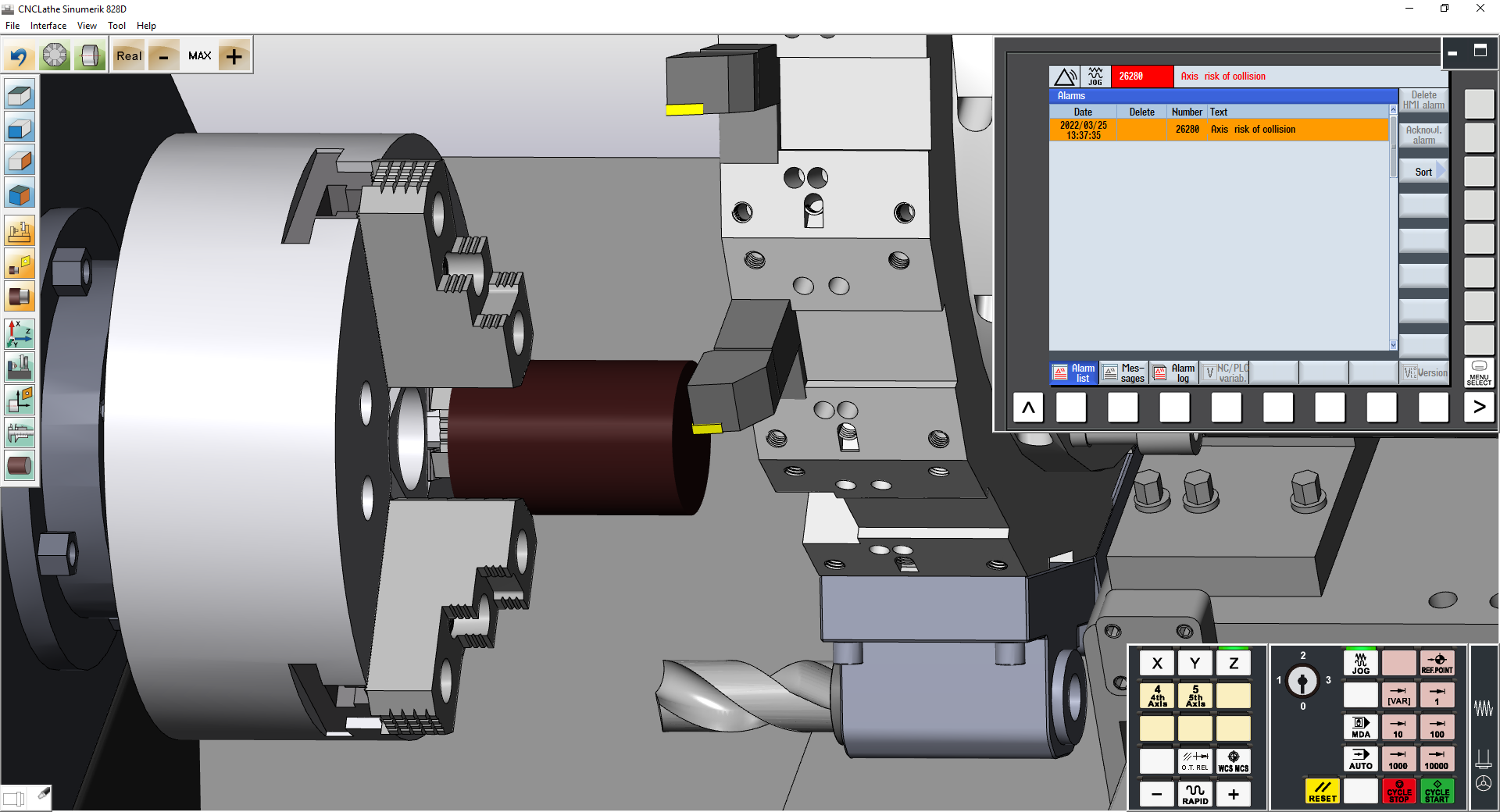
3.04 Simulation speed adjustment: 100%, 160%, 250%, 500%
3.05 Workpiece setting
Max Diameter: 250mm
Max Length: 450mm
3.06 Turning Tool Setting: Diamond (80∘, 55∘,35∘),Triangle (60∘), Trigon(80∘), Thread, Groove, Round, Radius Corner Groove, Drill, Tap, Center Drill, End Mill
3.07 Magazine install: Tool install, modify, delete
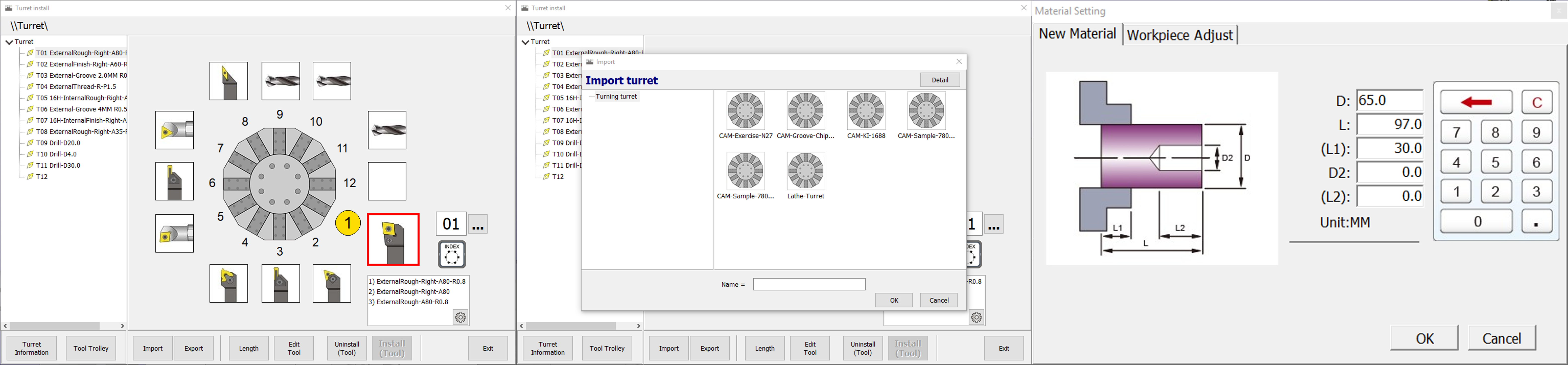
3.08 Standard view : Top (XY), Front (ZX), Side, (YZ), Isometric (ISO)
3.09 Fixed view setting: Material range, Machine bed range, Machine range
3.10 Operator view: Shift, Rotate, Zoom in/out
Standard Version Features (included)
3.21 Based on 3D physical construction, the machine model of Horizontal Turning-Single spindle and turret, including: machine bed, spindle head, chuck, jaw, turret, tool, tailstock, live center
3.22 Simulated design including coolant fluid, cutting the workpiece until chips spattering, audio (tool movement, cutting sound effect, spindle rotation, alarm)
3.23 Collision detection: tool and material, jaw, collision detection
3.24 Simulation Speed Adjustment: 50%, 100%, 250%, 500%
3.25 Workpiece linear measurement function: diameter, thickness, length
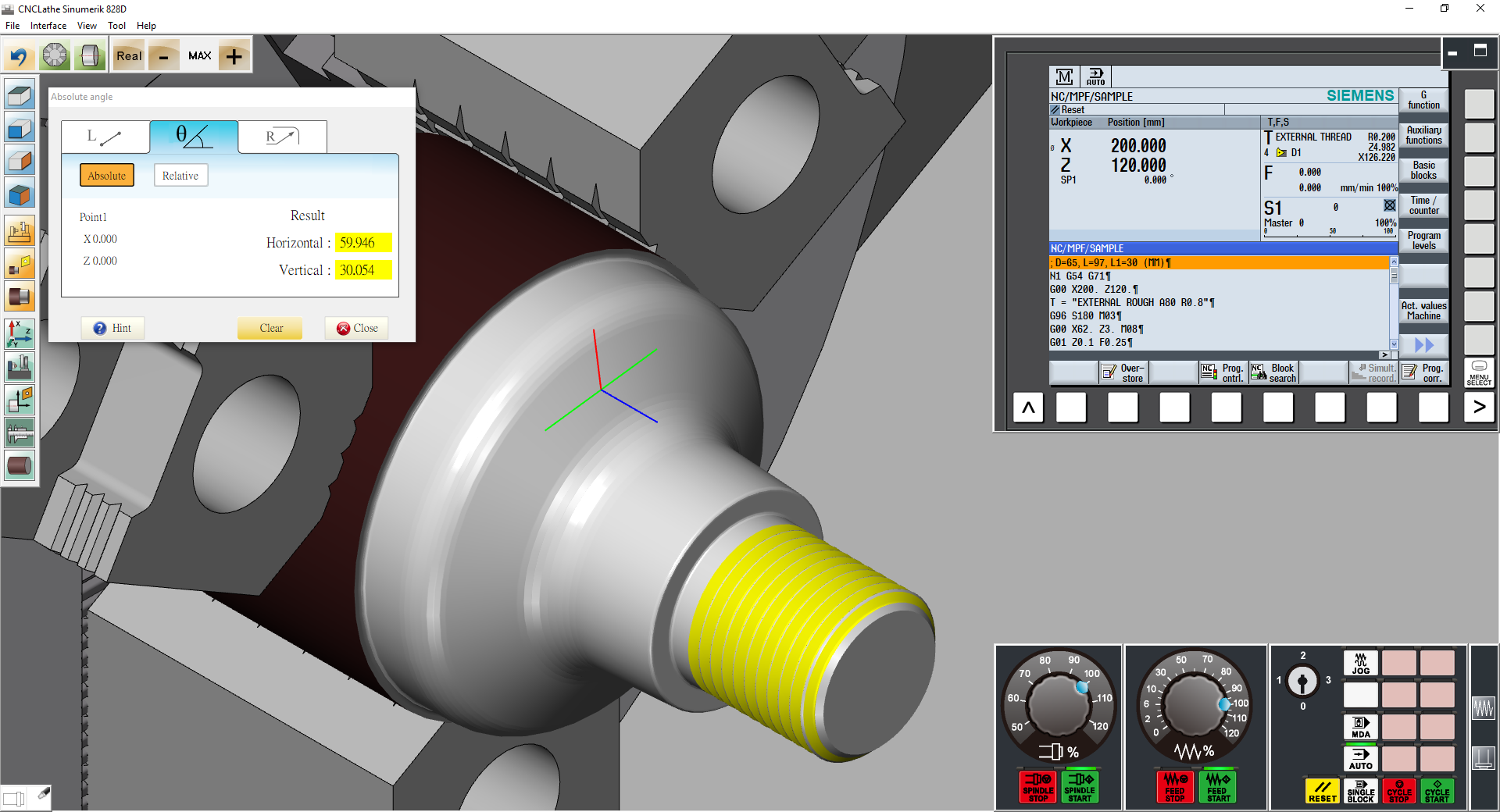
3.26 Quick reset to Factory Setting
3.27 CNC Program Import/Export function
Professional Version Additional Features
3.31 Based on 3D physical construction,
the machine model of Horizontal Turning-Single spindle and turret
includes machine bed, metal shell, auto-door, spindle head, chuck, jaw, turret, tool, tailstock, live center
3.32 Machine case display/hide
3.33 Program zero point display according to tool offset value
3.34 Save and import configuration to completely save and resume the settings status as a reference of examination and correction
3.35 Workpiece material: save and load in (format: STL)
3.36 Workpiece material setting: inner hole dimension setting, jaw setting
3.37 Tool setting: add, modify, delete, tool data import/export
3.38 Magazine Install: Import/Export, Common Magazine
3.39 Simulation Speed Adjustment: 10%, 50%, 100%, 160%, 250%, 500%, 900%, 990%, MAX
3.40 Limit the simulation speed within the range of 500% to help students with their program check and execution
3.41 Workpiece dimension measure: angle measurement (Absolute, both sides angle), arc(three points circle)
3.42 Equipped with machine produce status and immediate monitoring management system
3.43 Collision detection:
Tool and material, jaw, spindle, tailstock. collision detection
Turret and material, jaw, spindle, tailstock. collision detection
4 CNC Turning Program Simulation
4.01 G Code function
(1) Interpolation: G00 G01 G02 G03 G04 G33
(2) Dwell: G04
(3) Plane Selection: G17 G18 G19
(4) Tool Radius Compensation Command: G40 G41 G42
(5) Input system inches/metric: G70 G71
(6) Absolute/Incremental Dimension:G90 G91
(7) Reference point approach: G74, Fixed point approach: G75
(8) Feed Rate Command: G94 G95
(9) Cutting rate command: G96 G97
(10) Adjustable work offset: SUPA G53 G54, G55, G56, G57
(11) Turning Cycle: CYCLE92 (cut-off), CYCLE930(groove), CYCLE951 (stock removal), CYCLE99(thread turning)
(12) Drilling Cycle: CYCLE81, CYCLE82, CYCLE83
(13) Tapping Cycle: CYCLE84, CYCLE840
(14) Reaming Cycle: CYCLE 85
(15) Boring Cycle: CYCLE86
4.02 M Code auxiliary function
(M00) Program stop (M03) Spindle forward
(M01) Optional stop (M04) Spindle reversal
(M02) End of program (M05) Spindle stop
(M06) Auto tool change
(M30) End of program
Standard Version Features (included)
4.21 G Code function:
(16) Support Chamfer the count corner and Round the count corner
4.22 M Code auxiliary function
(M08) Coolant fluid on (M09) Coolant fluid off
Professional Version Additional Features
4.31 G Code function:
(17) Support G01 A angle(ANG)command function
(18) Support G291 ISO command form
4.32 MACRO function
(1) Program Variable – User variable
(2) Arithmetic Command
addition +, subtraction -, multiplication x, division /
SIN, COS, TAN, SQRT square root, ABS Absolute value
(3) Logic Operations
equal to==, not equal to<>, greater than>, less than <,
greater than or equal to>=, less than or equal to<=
(4) Conditional Branches–
(a) Jump GOTO n
(b) Conditional Jump IF [conditional] GOTO n
(c) Conditional loop WHILE [conditional]